How AHF uses Stability Testing in our Supplement Manufacturing
What is stability testing in supplement Manufacturing - and how does AHF ensure quality and efficacy
March 19, 2025
Stability testing is a fundamental process in the development of dietary supplements, and plays an essential role in establishing and ensuring the appropriate shelf life, storage conditions, and labeling instructions. This involves assessing a product’s resilience under specific packaging and storage conditions, among other factors.
The goal of stability testing is to safeguard consumers by scientifically proving that the dietary supplement being produced retains its claimed potency, purity, and physical characteristics over the intended period of time. Working with an NSF certified supplement manufacturer like American Health Formulations can help answer all of these questions, as well as determine if improvements can be made to the product’s formula.
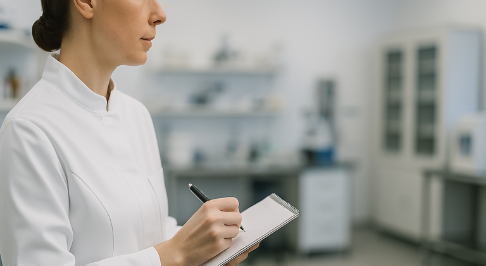
Why is Stability Testing Important for Supplement Brands?
Ensures Consumer Safety and Product Efficacy
Dietary supplement stability studies help determine how a product’s quality and characteristics may change over time. Both active and inactive ingredients in a supplement may degrade, potentially leading to reduced potency (impacting efficacy) and undesirable metabolites or tablet/capsule frailty (impacting safety). Stability testing assures that the supplement maintains its original safety and efficacy.Setting a Scientifically Backed Expiration Date
Consumers rely on expiration dates to ensure they are using a product that is still effective. Stability testing provides the scientific data necessary to establish and support these dates, assuring consumers that the nutraceuticals in the supplement will maintain their potency until the indicated time. It’s important to note that while the FDA doesn’t require expiration dates, if a product does have one, the FDA recommends having data from a written testing program to support it.Reducing the Risk of Product Recalls and Lawsuits
The degradation of ingredients can lead to product recalls. By ensuring the stability of their products, brands can significantly reduce this risk and the associated financial and reputational damage.Providing Data for Optimizing Packaging and Storage Recommendations
This allows manufacturers to assess whether the packaging is suitable for protecting the product from factors like light, moisture, and oxygen, and to determine appropriate storage conditions to recommend to consumers. For instance, light-protective bottles might be necessary for certain light-sensitive ingredients.Building Brand Trust and Consumer Confidence
Demonstrating a commitment to product quality and efficacy through stability testing fosters trust and loyalty among consumers. In today’s market, where consumers are increasingly informed and scrutinizing product quality, this due diligence is becoming a significant differentiator.Factors That Affect Product Stability
- Temperature: This is a critical factor, as increased temperatures can accelerate chemical degradation. A seemingly small increase of 10°C can significantly speed up hydrolytic degradation.
- Humidity: Moisture can also negatively impact stability, causing tablets to become porous or lose their tensile strength, especially those containing fillers like microcrystalline cellulose (MCC).
- Light: Exposure to light can lead to reduced efficacy or inactivation of certain ingredients.
- Oxygen: Oxygen can cause chemical instability, leading to degradation and the formation of impurities.
- pH: The acidity or alkalinity of the product’s environment can trigger chemical reactions that degrade active ingredients or affect their release.
- Ingredient Interactions: The combination of multiple active ingredients can lead to cross-reactions that affect stability. Multivitamin supplements, with their wide array of vitamins, often require careful stability evaluation.
- Dosage Form: Capsules, tablets, and powders have different characteristics and may require different excipients (inactive ingredients) that can influence stability.
- Packaging Materials: The type of container and closure used can affect how well the supplement is protected from environmental factors.
How is Stability Testing Done?
- Accelerated Stability: This involves storing the packaged supplement in a stability chamber under controlled, elevated temperature and humidity conditions. These harsh conditions are designed to accelerate the normal aging process, allowing manufacturers to get an estimate of shelf life in a shorter period. For example, one month in an accelerated chamber might approximate six months of aging under normal conditions.
- Ambient Stability (Real-Time Stability): This method involves storing samples of the finished, packaged product under normal, controlled room temperature, and humidity conditions in a retain room for the anticipated shelf life. Ambient or “real-time” stability studies simulate the expected storage conditions and run for the anticipated shelf life of the product. Products are periodically pulled from the retain room and tested to confirm the results obtained from accelerated testing.
Common Tests Conducted During Stability Testing
- Sensory/Organoleptic Evaluation: This assesses physical attributes like taste, flavor, color, odor, and appearance, which can indicate degradation.
- Chemical Analysis: Techniques such as High-Performance Liquid Chromatography (HPLC) are used to separate and quantify the active ingredients, ensuring they meet the labeled amounts. Mass Spectrometry (MS) can be used to determine the molecular weight and identify any unknown degradation in products.
- Physical Analysis: This involves evaluating physical properties like tablet hardness, friability (tendency to crumble), and powder flowability. Dissolution testing measures how effectively tablets and capsules dissolve, mimicking digestion.
- Microbiological Examination: Supplements are tested to ensure they do not contain harmful levels of microorganisms like E. coli.
How AHF uses stability testing in our supplement manufacturing
American Health Formulations (AHF) is an NSF certified supplement manufacturer that offers on-site stability studies for dietary supplements and trend analysis as part of our extensive research and product development capabilities.
Through trend analysis and the evaluation of a product’s degradation and oxidation rate under several temperatures, humidities, and time points, AHF’s R&D scientists and method developers can determine if further improvements can be made to your product’s formula. This valuable data supports their strategies in choosing the proper overages and excipients to ensure the best possible version of the product and manufacturing experience. Adding appropriate overages of certain nutrients can help ensure that label claims are met throughout the product’s shelf life.
AHF’s on-site stability testing services offer the advantage of obtaining data as early as the pre-production R&D batch stage, eliminating the need to wait several months for results from a costly third-party stability lab. Furthermore, the product’s trend analysis will be most accurate because it’s conducted in-house.
Why Choose American Health Formulations?
American Health Formulations (AHF) a leading provider of dietary supplement contract manufacturing services, including:
- Custom Supplement Manufacturing: Tailored formulations to meet your brand’s unique needs.
- Private Label Supplement Manufacturing: Market-ready, pre-developed formulations.
- Multiple Dosage Forms and Co-Packaging options:
- Analytical Testing & Stability Studies: On-site laboratories to support meeting cGMP regulatory requirements in purity, safety and product effectiveness.
- Graphic Design and Labeling: In-house graphic design team for labels and pouches to be professionally designed and printed.
Contact American Health Formulations today to learn how our expertise as a custom supplement manufacturer can help grow your health and wellness brand.